EV Batteries: The First European Industrial-Scale Recycling Plant Opens
Mercedes-Benz has opened a recycling facility capable of processing 2,500 tonnes of material. The plant will use recovered materials to produce 50,000 new batteries.
On October 21, Mercedes-Benz opened the first industrial-scale plant for recycling lithium-ion batteries based in Europe. The facility covers 6,800 square meters and is entirely powered by green energy, including a rooftop solar installation with a peak capacity of over 350 kilowatts. This plant is located in Kuppenheim, about an hour from Stuttgart, and will have an annual recycling capacity of 2,500 tonnes of material, which will then be reused to produce 50,000 batteries for the German group's electric models. "A fundamental milestone towards improving the sustainability of raw materials," said Mercedes CEO Ola Källenius at the plant's inauguration, which was attended by German Chancellor Olaf Scholz, emphasising the significance of this ground-breaking first step in the automotive electrification industry. "The circular economy is a growth driver and, at the same time, an essential element in achieving our climate goals," Scholz stated during the presentation. This news from Germany is consistent with the European decision to stop registering petrol and diesel vehicles in 2035, in pursuit of Green Deal targets that emphasise sustainable production and recycling of electric car batteries.
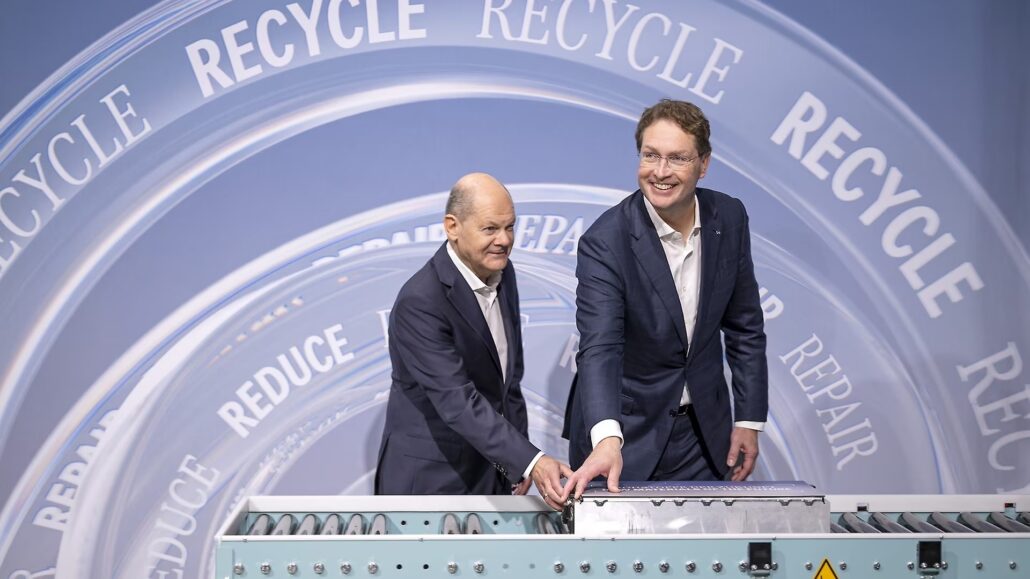
The battery recycling plant can recover 96% of the materials.
The Kuppenheim plant aims to recycle more than 96% of materials by treating the batteries mechanically and hydro metallurgically simultaneously. Plastics, copper, aluminium, and iron are all sorted and separated in the first step. The second process extracts precious metals such as cobalt, nickel, and lithium, which are used to make cell electrodes. According to Mercedes, this process consumes less energy and produces less waste than other facilities in Europe, and it can cover all stages of the process, from crushing battery modules to drying and processing materials.
Mercedes-Benz's technology partner for the plant is Primobius, a joint venture between SMS Group, a German engineering and plant construction company, and Neometals, an Australian process technology developer. The plant is also funded by Germany's Federal Ministry for Economic Affairs and Climate Action as part of a scientific research collaboration with three German universities. Recycling, in addition to reducing waste from electric vehicles, is seen as critical for strengthening European sovereignty in the battery sector, as materials such as cobalt, nickel, and lithium are largely sourced from outside the region.
German plant serves as Europe's central hub for battery recycling.
The recycling plant, which was completed in less than two years, will serve not only the renowned German brand's vehicles but is also expected to become a key facility on a continental scale. European manufacturers are constantly looking for critical raw materials, which are frequently sourced from China. However, Europe hopes to reduce its reliance on these imports in order to achieve its decarbonisation goals. Recycling is the only way forward. "To produce batteries sustainably and resourcefully, recycling is essential," emphasised German Chancellor Olaf Scholz once more.
Share your remanufacturing stories with us
Do you have an innovation, research results or an other interesting topic you would like to share with the remanufacturing industry? The Rematec website and social media channels are a great platform to showcase your stories!
Please contact our Brand Marketing Manager.
Are you an Rematec exhibitor?
Make sure you add your latest press releases to your Company Profile in the Exhibitor Portal for free exposure.